Réparer, Renforcer ou Remplacer : Que faire avec les racks de stockage et rack à palettes endommagés ?
Guide pratique
Réparer, Renforcer ou Remplacer : Que faire avec les racks de stockage et rack à palettes endommagés ?
Dans le monde dynamique de la logistique et de l'entreposage, les racks de stockage représentent l'épine dorsale de toute opération efficace. Ces structures métalliques robustes permettent d'optimiser l'espace vertical, d'organiser méthodiquement les marchandises et de faciliter la gestion des stocks. Toutefois, malgré leur conception solide, les racks à palettes subissent inévitablement des dommages au fil du temps. Les chocs causés par les chariots élévateurs, la surcharge des rayonnages ou simplement l'usure naturelle peuvent compromettre l'intégrité structurelle de ces équipements essentiels.
Face à un rack de stockage endommagé, trois options principales s'offrent aux gestionnaires d'entrepôts : la réparation, le renforcement ou le remplacement complet. Ce choix, loin d'être anodin, peut avoir des répercussions considérables tant sur le plan financier que sur la sécurité des opérations. En effet, un rack défectueux représente un danger potentiel pour les marchandises stockées ainsi que pour le personnel qui évolue quotidiennement dans l'entrepôt. Par ailleurs, les interruptions d'activité liées à la maintenance des rayonnages industriels engendrent des coûts indirects qu'il convient de minimiser.
Dans ce contexte, la réparation des racks de stockage s'impose souvent comme une solution particulièrement avantageuse. Des entreprises spécialisées comme ROS France, leader dans ce domaine, proposent des méthodes innovantes permettant de restaurer la capacité de charge d'origine des rayonnages endommagés. Grâce à des certifications reconnues telles que DEKRA, ces interventions garantissent un niveau de sécurité optimal tout en offrant des économies substantielles par rapport au remplacement.
Néanmoins, dans certaines situations, le renforcement préventif ou le remplacement complet peuvent s'avérer plus appropriés. Comment déterminer la meilleure approche pour votre cas spécifique ? Quels sont les critères à prendre en compte ? Quels avantages et inconvénients présente chaque option ? Découvrez notre analyse comparative sur la page Remplacer ou réparer.
Cet article vous propose un examen approfondi des différentes solutions disponibles pour gérer les racks endommagés. Nous analyserons en détail les processus de réparation, les méthodes de renforcement et les cas où le remplacement s'impose comme la seule alternative viable. En outre, nous vous fournirons des outils décisionnels pratiques pour vous aider à faire le choix le plus judicieux en fonction de votre situation particulière.
Que vous soyez responsable logistique, gestionnaire d'entrepôt ou simplement soucieux d'optimiser la sécurité et la durabilité de vos installations de stockage, cette analyse vous permettra d'aborder la question des racks endommagés avec une vision claire et complète des enjeux et des solutions disponibles.
Tableau comparatif : Réparation vs Renforcement vs Remplacement des racks de stockage
Critères | Réparation | Renforcement | Remplacement |
---|---|---|---|
Coût relatif | Économie jusqu'à 80% par rapport au remplacement | Variable selon l'étendue, généralement 30-50% du coût de remplacement | Coût le plus élevé (investissement initial important) |
Délai d'intervention | Rapide (quelques heures à 1-2 jours) | Modéré (1-3 jours selon l'étendue) | Long (plusieurs jours à plusieurs semaines) |
Impact sur l'activité | Minimal (possibilité d'intervention sans déchargement avec ROS France) | Limité (intervention possible sur zones spécifiques) | Important (nécessite déchargement complet des zones concernées) |
Durabilité de la solution | Bonne (restauration des propriétés mécaniques d'origine, certifiée DEKRA) | Très bonne (amélioration de la résistance par rapport à l'état d'origine) | Excellente (structures neuves aux normes les plus récentes) |
Impact environnemental | Faible (économie jusqu'à 50% d'émissions CO2 vs remplacement) | Modéré (utilisation limitée de nouveaux matériaux) | Élevé (production, transport et installation de nouvelles structures) |
Cas d'application idéaux | Dommages localisés de niveau vert ou jaune, structures récentes en bon état général | Zones à risque élevé, prévention, adaptation à de nouvelles charges | Dommages multiples/sévères, structures obsolètes, changement majeur des besoins |
Garanties | Certification DEKRA/Bureau Veritas (pour ROS France), garantie écrite | Variable selon prestataire, généralement 1-2 ans | Garantie fabricant complète (généralement 3-5 ans) |
Flexibilité | Limitée (restauration de l'existant) | Modérée (amélioration des caractéristiques existantes) | Maximale (reconfiguration complète possible) |
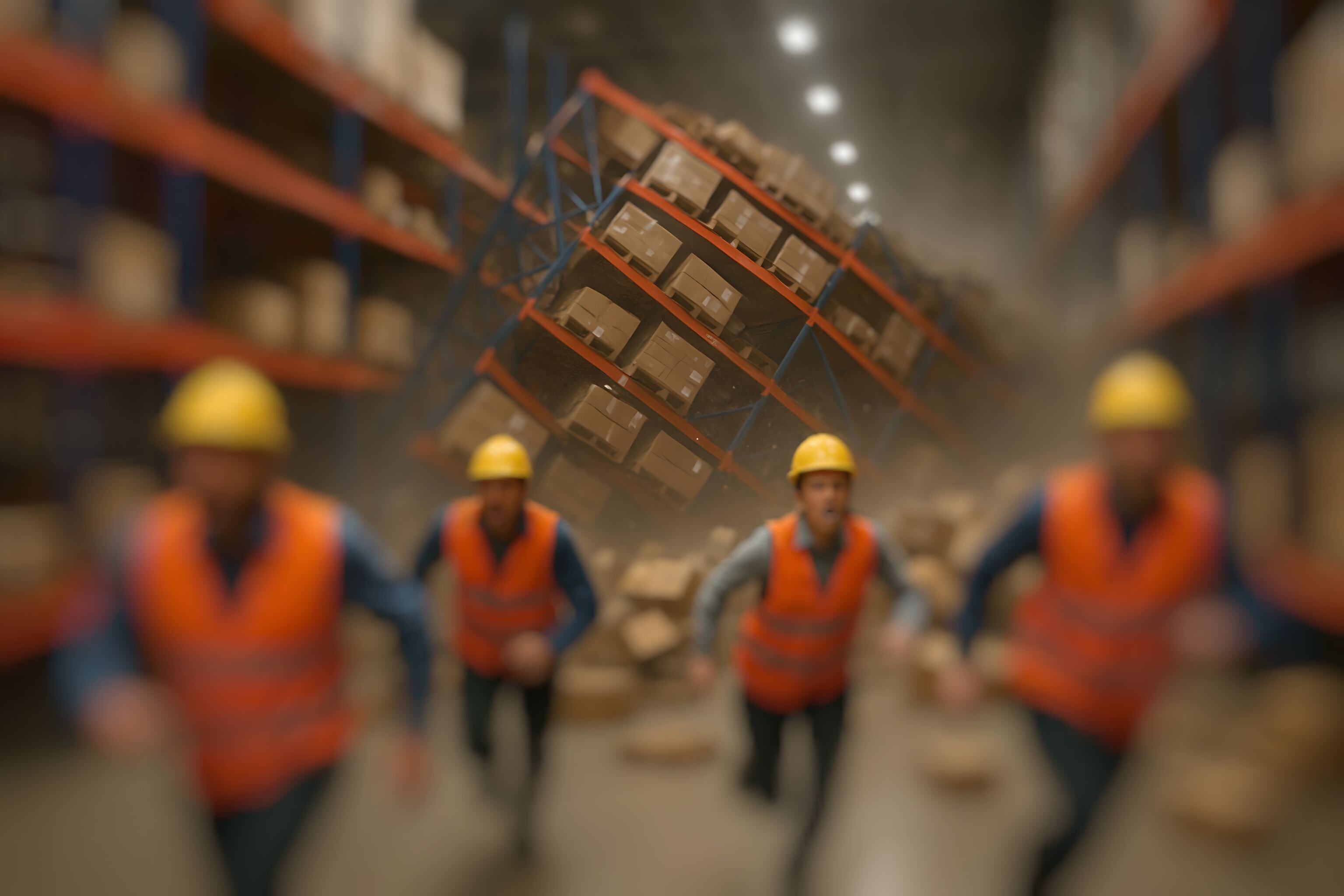
1. Les racks de stockage : éléments essentiels de la logistique moderne
Dans l'univers complexe de la logistique moderne, les racks de stockage constituent des éléments fondamentaux pour toute entreprise gérant des flux de marchandises. Ces structures métalliques, souvent méconnues du grand public, représentent pourtant un maillon crucial dans la chaîne d'approvisionnement mondiale. En effet, sans ces systèmes de rangement efficaces, l'organisation des entrepôts serait chaotique et l'optimisation de l'espace pratiquement impossible.
Définition et types de racks de stockage
Un rack de stockage est une structure métallique conçue pour supporter et organiser des charges de manière verticale, permettant ainsi d'exploiter pleinement la hauteur disponible dans un entrepôt. Cette définition, bien que simple, englobe en réalité une grande diversité de systèmes adaptés à des besoins spécifiques. Parmi les plus courants, nous retrouvons les racks à palettes, également appelés palettiers, qui constituent la solution privilégiée pour le stockage de marchandises palettisées. Ces structures robustes peuvent supporter des charges considérables, allant jusqu'à plusieurs tonnes par niveau.
Par ailleurs, les rayonnages industriels offrent une alternative plus polyvalente, permettant le stockage de produits de différentes tailles et formes. Ces systèmes sont particulièrement appréciés dans les environnements nécessitant un accès fréquent aux marchandises. En outre, les cantilevers, caractérisés par leurs bras en porte-à-faux, sont spécialement conçus pour les charges longues comme les tuyaux, les planches ou les profilés métalliques.
Les racks dynamiques, quant à eux, intègrent des rouleaux ou des rails permettant le déplacement automatique des palettes selon le principe du FIFO (First In, First Out). Cette solution optimise la rotation des stocks et s'avère particulièrement adaptée aux produits périssables. Enfin, les racks d'accumulation ou drive-in permettent un stockage dense en profondeur, maximisant ainsi l'utilisation de l'espace disponible.
Importance des racks dans l'optimisation de l'espace et la gestion des stocks
L'avantage principal des racks de stockage réside dans leur capacité à exploiter la dimension verticale des entrepôts. En effet, ces structures permettent d'empiler les marchandises sur plusieurs niveaux, multipliant ainsi la surface de stockage disponible. Par conséquent, une installation bien conçue peut augmenter considérablement la capacité de stockage sans nécessiter d'extension des locaux, ce qui représente une économie substantielle pour les entreprises.
En outre, les racks de stockage facilitent grandement la gestion des stocks. Grâce à une organisation méthodique des emplacements, les opérateurs peuvent localiser rapidement les produits recherchés, réduisant ainsi le temps consacré à la préparation des commandes. De plus, cette visibilité accrue permet un inventaire plus précis et une meilleure traçabilité des marchandises. Par ailleurs, les systèmes modernes de gestion d'entrepôt (WMS) s'appuient sur cette organisation spatiale pour optimiser les flux logistiques et minimiser les déplacements inutiles.
Toutefois, pour tirer pleinement parti de ces avantages, il est essentiel de choisir le type de rack adapté à ses besoins spécifiques. En effet, une solution inadaptée peut non seulement compromettre l'efficacité opérationnelle, mais également engendrer des risques pour la sécurité des biens et des personnes.
Quels sont les composants principaux d'un rack de stockage ?
Pour comprendre les enjeux liés à la réparation et à l'entretien des racks de stockage, il est nécessaire de connaître leurs composants principaux. Un rack à palettes standard se compose essentiellement de montants d'échelles, de lisses, de traverses et de diagonales.
Les montants d'échelles constituent les éléments verticaux qui supportent l'ensemble de la structure. Ces profilés métalliques, généralement perforés pour permettre l'ajustement des niveaux, sont particulièrement exposés aux chocs des engins de manutention. Les échelles endommagées sont formées par l'assemblage de deux montants reliés par des traverses et des diagonales, créant ainsi un cadre rigide capable de supporter des charges importantes.
Les lisses, quant à elles, sont les éléments horizontaux sur lesquels reposent directement les palettes. Fixées aux montants par des connecteurs spécifiques, elles déterminent la capacité de charge de chaque niveau. Leur résistance dépend non seulement de leur section, mais également de la qualité de leur connexion avec les montants.
D'autres éléments peuvent compléter ces composants de base, comme les platelages métalliques qui permettent le stockage de produits non palettisés, les protections d'échelles qui préviennent les dommages causés par les chariots élévateurs, ou encore les grilles anti-chute qui empêchent la chute accidentelle de marchandises.
Chacun de ces composants joue un rôle crucial dans la stabilité et la sécurité globale du système. Par conséquent, tout dommage affectant l'un d'entre eux peut potentiellement compromettre l'intégrité de l'ensemble de la structure.
Normes et réglementations applicables aux racks de stockage
La sécurité des installations de stockage est encadrée par plusieurs normes et réglementations strictes. En Europe, la série de normes EN 15635 définit les principes d'utilisation et de maintenance des systèmes de stockage statiques en acier. Cette norme, particulièrement importante, établit notamment les critères d'évaluation des dommages et les procédures d'inspection périodique.
Par ailleurs, la norme NF EN 15512 précise les principes de calcul des structures, tandis que la NF EN 15620 définit les tolérances, déformations et jeux fonctionnels acceptables. La norme NF EN 15629, quant à elle, spécifie les exigences techniques pour la conception des systèmes de stockage.
En France, ces normes sont complétées par les dispositions du Code du travail, qui impose à l'employeur une obligation générale de sécurité. L'article L4321-1 stipule notamment que les équipements de travail doivent être installés, utilisés et maintenus de manière à préserver la santé et la sécurité des travailleurs.
Le respect de ces normes n'est pas seulement une obligation légale, mais également une garantie de sécurité pour les opérateurs et les marchandises. Des organismes comme DEKRA ou Bureau Veritas proposent des certifications attestant de la conformité des installations ou des réparations certifiées. Ces certifications, comme celle obtenue par ROS France pour ses méthodes de réparation, offrent une assurance supplémentaire quant à la fiabilité des solutions mises en œuvre.
Les racks de stockage représentent donc bien plus que de simples étagères industrielles. Ces structures complexes, soumises à des contraintes importantes, nécessitent une attention particulière tout au long de leur cycle de vie. Toutefois, malgré toutes les précautions prises lors de leur conception et de leur installation, ces équipements restent vulnérables face aux aléas quotidiens d'un entrepôt en activité. Mais que faire lorsque ces structures essentielles sont endommagées ? Comment évaluer la gravité des dégâts et déterminer la meilleure marche à suivre ? C'est ce que nous allons explorer dans le chapitre suivant.
"La réparation des racks de stockage sans déchargement représente une innovation majeure dans notre secteur. Cette approche permet non seulement de réduire considérablement les coûts directs, mais également d'éliminer presque totalement les perturbations opérationnelles, un avantage crucial dans les environnements logistiques à flux tendu."
2. Causes et conséquences des dommages sur les racks de stockage
Dans l'environnement dynamique d'un entrepôt, les racks de stockage sont constamment exposés à divers risques susceptibles d'altérer leur intégrité structurelle. Comprendre les causes et les conséquences de ces dommages constitue une étape essentielle pour mettre en place des stratégies de maintenance efficaces et garantir la sécurité des installations. En effet, un rack endommagé représente non seulement un risque pour les marchandises stockées, mais également pour le personnel qui évolue quotidiennement dans ces espaces.
Principales causes de dommages sur les racks de stockage
Les impacts de chariots élévateurs figurent parmi les causes les plus fréquentes de détérioration des racks de stockage. Malgré la formation des caristes et les mesures de prévention, les manœuvres dans des allées parfois étroites peuvent entraîner des collisions avec les structures. Ces chocs, même à faible vitesse, peuvent provoquer des déformations significatives des montants d'échelles, particulièrement vulnérables à leur base. En outre, les fourches des engins de manutention peuvent également endommager les lisses lors des opérations de dépose ou de prise des palettes.
La surcharge constitue une autre cause majeure de dommages. Chaque composant d'un rack est conçu pour supporter une charge maximale spécifique. Toutefois, dans la pratique, ces limites peuvent être dépassées, soit par méconnaissance des capacités réelles, soit par une volonté d'optimiser l'espace disponible. Cette surcharge engendre des contraintes excessives sur les structures, pouvant conduire à des déformations permanentes, voire à des ruptures de composants. Par ailleurs, une répartition inégale des charges sur les lisses peut amplifier ce phénomène en créant des points de concentration de contraintes.
L'usure naturelle des matériaux contribue également à l'affaiblissement des racks de stockage au fil du temps. Les cycles répétés de chargement et de déchargement, les vibrations causées par les équipements de manutention, ainsi que les conditions environnementales (humidité, variations de température) peuvent altérer progressivement les propriétés mécaniques des composants métalliques. Cette dégradation, bien que moins visible que les dommages causés par des impacts directs, n'en demeure pas moins préoccupante pour la sécurité globale de l'installation.
Enfin, des erreurs lors du montage initial ou des modifications ultérieures peuvent compromettre la stabilité des rayonnages. L'absence de certains éléments de contreventement, le mauvais positionnement des connecteurs ou l'utilisation de composants non compatibles sont autant de facteurs susceptibles d'affaiblir la structure et d'augmenter sa vulnérabilité face aux contraintes quotidiennes.
Comment identifier les dommages sur les racks de stockage ?
Pour faciliter l'évaluation des dommages et la prise de décision concernant les mesures correctives à mettre en œuvre, la norme européenne NF EN 15635 établit une classification en trois niveaux de gravité, symbolisés par un code couleur : vert, jaune et rouge.
Les dommages de niveau vert correspondent à des déformations légères qui ne compromettent pas immédiatement la capacité de charge ou la stabilité de la structure. Ces dommages doivent être surveillés lors des inspections régulières, mais ne nécessitent pas d'intervention immédiate. Toutefois, il est recommandé de planifier leur réparation dans le cadre d'un programme de maintenance préventive, afin d'éviter leur aggravation.
Les dommages de niveau jaune, ou orange selon certaines classifications, indiquent un état dangereux nécessitant une intervention rapide. Dans cette catégorie, on retrouve notamment les déformations de montants comprises entre 3 et 5 mm, les déformations de lisses supérieures à 5 mm, ou encore les connecteurs partiellement désengagés. Ces dommages, bien que n'imposant pas un déchargement immédiat, doivent être traités dans les plus brefs délais pour éviter toute dégradation supplémentaire.
Enfin, les dommages de niveau rouge signalent un danger imminent et requièrent une action immédiate. Il s'agit notamment des déformations de montants supérieures à 5 mm, des ruptures de soudures, ou des connecteurs complètement désengagés. Dans ces situations, le déchargement de la zone concernée s'impose avant toute intervention, afin de prévenir tout risque d'effondrement.
Cette classification, bien qu'utile comme cadre de référence, ne remplace pas l'expertise d'un professionnel qualifié. En effet, l'évaluation précise des dommages nécessite une connaissance approfondie des structures de rayonnages et de leur comportement mécanique. Des entreprises spécialisées comme ROS France proposent des services d'inspection permettant d'identifier avec précision la nature et la gravité des dommages, ainsi que les solutions de réparation les plus adaptées.
Risques associés aux racks endommagés
Les conséquences d'un rack endommagé peuvent être considérables, tant sur le plan humain que matériel et financier. Le risque le plus grave est sans conteste l'effondrement partiel ou total de la structure. Un tel événement peut entraîner des blessures graves, voire mortelles, pour le personnel présent dans la zone. Par ailleurs, les marchandises stockées peuvent être détruites ou endommagées, générant des pertes financières directes potentiellement importantes.
Au-delà de ces conséquences immédiates, un effondrement de rayonnages peut également provoquer un effet domino, affectant des structures adjacentes initialement intactes. Ce phénomène, particulièrement préoccupant dans les installations denses, peut amplifier considérablement l'étendue des dégâts et des perturbations opérationnelles.
Sur le plan juridique, la responsabilité de l'employeur peut être engagée en cas d'accident lié à un défaut de maintenance des équipements. L'article L4321-1 du Code du travail impose en effet une obligation générale de sécurité concernant les équipements de travail, dont font partie les racks de stockage. Le non-respect de cette obligation peut entraîner des sanctions pénales, notamment en cas d'accident corporel.
Enfin, les perturbations opérationnelles consécutives à un incident peuvent générer des coûts indirects significatifs : interruption de l'activité, réorganisation temporaire des flux logistiques, mobilisation de ressources pour la gestion de crise, etc. Ces coûts, bien que difficiles à quantifier précisément, doivent être pris en compte dans l'évaluation globale des risques associés aux racks endommagés.
Importance de l'inspection régulière des racks
Face à ces risques, l'inspection régulière des racks de stockage s'impose comme une mesure préventive essentielle. La norme NF EN 15635 recommande la mise en place d'un programme d'inspection structuré, comprenant trois niveaux complémentaires.
L'inspection visuelle quotidienne, réalisée par les opérateurs dans le cadre de leurs activités habituelles, constitue la première ligne de défense. Bien que sommaire, ce contrôle régulier permet de détecter rapidement les anomalies évidentes, telles que les déformations importantes ou les éléments manquants.
L'inspection hebdomadaire, plus approfondie, est généralement effectuée par un responsable d'entrepôt ou un chef d'équipe. Elle vise à identifier systématiquement les dommages de niveau vert ou jaune, afin de planifier les interventions nécessaires avant que la situation ne se dégrade davantage.
Enfin, l'inspection annuelle, réalisée par un expert qualifié, permet une évaluation complète et détaillée de l'état des installations. Cette inspection, qui peut être confiée à un organisme externe comme DEKRA ou Bureau Veritas, donne lieu à un rapport détaillé identifiant les non-conformités et recommandant les actions correctives appropriées.
Pour faciliter ces inspections et assurer leur traçabilité, il est recommandé de mettre en place un système de documentation rigoureux. Des fiches d'inspection standardisées, des photographies des dommages identifiés, ainsi qu'un registre centralisant l'historique des contrôles et des interventions constituent des outils précieux pour une gestion efficace de la maintenance des racks.
Par ailleurs, la formation du personnel à la détection des anomalies et à l'évaluation préliminaire des risques renforce considérablement l'efficacité de ce dispositif préventif. Des sessions de sensibilisation régulières permettent de maintenir un niveau de vigilance élevé et d'instaurer une véritable culture de la sécurité au sein de l'entrepôt.
Comprendre les causes et les conséquences des dommages sur les racks de stockage constitue donc une étape fondamentale dans la mise en place d'une stratégie de maintenance efficace. Cette connaissance permet non seulement d'identifier les risques potentiels, mais également de déterminer les mesures préventives et correctives les plus adaptées à chaque situation.
Mais que faire concrètement lorsqu'un rack est endommagé ? Quelles sont les options disponibles et comment choisir la plus appropriée ? La réparation représente souvent une solution avantageuse, comme nous allons le voir dans le chapitre suivant, qui explore en détail cette approche et ses bénéfices.
"La certification que nous avons accordée au procédé de réparation ROS atteste que les structures réparées retrouvent leurs propriétés mécaniques d'origine, voire les dépassent dans certains cas."
3. La réparation des racks : une solution économique et efficace
Face à des racks de stockage endommagés, la réparation s'impose souvent comme une solution particulièrement avantageuse, tant sur le plan économique qu'opérationnel. Cette approche, qui consiste à restaurer les propriétés mécaniques d'origine des composants détériorés, permet de prolonger significativement la durée de vie des installations tout en garantissant leur sécurité. Toutefois, pour être pleinement efficace, la réparation doit être réalisée selon des méthodes éprouvées et certifiées, comme celles développées par des entreprises spécialisées telles que ROS France.
ROS France le leader de la réparation en France
Dans le domaine de la réparation des racks de stockage, ROS France s'est imposé comme un acteur de référence sur le marché français. Cette entreprise, qui bénéficie d'une expérience de plus de 20 ans dans ce secteur spécifique, a développé des méthodes innovantes permettant de restaurer l'intégrité structurelle des rayonnages endommagés sans nécessiter leur déchargement préalable. Cette particularité représente un avantage considérable pour les entreprises, qui peuvent ainsi maintenir leur activité pendant les interventions.
La spécificité de ROS France réside notamment dans son procédé breveté de réparation des montants d'échelles. Cette technique, qui a fait l'objet de nombreux tests et validations, permet de traiter efficacement les déformations causées par les chocs de chariots élévateurs, sans compromettre la capacité de charge des structures. Par ailleurs, l'entreprise propose également des solutions pour la réparation des lisses, des connecteurs et des autres composants des systèmes de stockage.
Au-delà de son expertise technique, ROS France se distingue par son approche globale de la maintenance des racks. L'entreprise propose en effet un service complet, depuis l'inspection initiale jusqu'à la certification post-réparation, en passant par le diagnostic précis des dommages et la mise en œuvre des solutions adaptées. Cette vision intégrée permet d'assurer une cohérence dans la gestion de la sécurité des installations de stockage.
La certification DEKRA : garantie de qualité et de sécurité
L'un des atouts majeurs de ROS France réside dans la certification DEKRA obtenue pour ses méthodes de réparation. DEKRA, organisme indépendant reconnu internationalement dans le domaine de la certification et de l'inspection technique, a validé l'efficacité et la fiabilité du procédé ROS après une série de tests rigoureux. Cette certification constitue une garantie essentielle pour les entreprises qui confient la réparation de leurs racks à ROS France.
Concrètement, la certification DEKRA atteste que les réparations effectuées selon le procédé ROS permettent de restaurer la capacité de charge d'origine des structures, conformément aux exigences de la norme NF EN 15635. Elle confirme également que les composants réparés présentent une résistance mécanique équivalente, voire supérieure, à celle des éléments d'origine non endommagés.
Cette reconnaissance officielle s'avère particulièrement précieuse dans un contexte où la responsabilité des entreprises peut être engagée en cas d'accident lié à un défaut de maintenance des équipements. En effet, la certification DEKRA constitue un élément probant démontrant que toutes les mesures nécessaires ont été prises pour garantir la sécurité des installations.
Par ailleurs, ROS France bénéficie également d'une certification Bureau Veritas, qui complète la validation DEKRA et renforce encore la crédibilité de ses solutions. Cette double certification, rare dans le secteur, témoigne du niveau d'exigence élevé que s'impose l'entreprise dans le développement et la mise en œuvre de ses procédés de réparation.
Processus de réparation des racks sans déchargement
L'une des innovations majeures proposées par ROS France réside dans sa capacité à réparer les racks de stockage sans nécessiter leur déchargement préalable. Cette approche, qui contraste avec les méthodes traditionnelles, présente des avantages considérables en termes de continuité d'activité et de réduction des coûts indirects.
Le processus de réparation débute par une inspection détaillée des dommages, permettant d'évaluer leur nature et leur gravité selon la classification établie par la norme NF EN 15635. Cette étape cruciale détermine la faisabilité d'une réparation sans déchargement et les techniques spécifiques à mettre en œuvre. Dans certains cas, notamment pour les dommages de niveau rouge particulièrement sévères, un déchargement partiel peut néanmoins s'avérer nécessaire pour garantir la sécurité de l'intervention.
Après l'intervention, une vérification complète est réalisée pour s'assurer que la réparation répond aux standards de qualité requis. Cette étape comprend notamment des contrôles dimensionnels et des tests de charge, conformément aux exigences des certifications DEKRA et Bureau Veritas.
Enfin, après vérification de la conformité de l'intervention, un certificat de sécurité écrit est délivré, attestant que la réparation a été effectuée selon les standards requis et que la structure peut être utilisée en toute sécurité. Ce document, qui s'intègre dans le dossier de maintenance de l'installation, peut s'avérer précieux en cas de contrôle ou d'audit de sécurité.
Il est important de souligner que ce processus de réparation sans déchargement présente un avantage considérable en termes de continuité d'activité. En effet, les perturbations opérationnelles sont minimisées, permettant à l'entrepôt de maintenir un niveau de productivité quasi normal pendant toute la durée de l'intervention.
Pourquoi choisir la réparation des racks de stockage ?
Sur le plan financier, la réparation des racks de stockage offre des avantages substantiels par rapport au remplacement complet. Selon les données fournies par ROS France, l'économie réalisée peut atteindre 80% du coût de remplacement des montants endommagés. Cette différence significative s'explique par plusieurs facteurs.
Tout d'abord, le coût des matériaux est considérablement réduit, puisque seuls les éléments de réparation sont nécessaires, et non des échelles complètes. De plus, l'absence de démontage et de remontage des structures existantes permet d'économiser de nombreuses heures de main-d'œuvre, ce qui se traduit directement par une diminution des coûts d'intervention.
Par ailleurs, la possibilité de réaliser les réparations sans déchargement des rayonnages élimine les coûts indirects liés à la manutention des marchandises et à leur stockage temporaire. Ces opérations, souvent sous-estimées dans les évaluations initiales, peuvent représenter une part significative du budget global d'un remplacement.
Au-delà des économies directes, la réparation permet également de réduire considérablement les perturbations opérationnelles. En effet, contrairement au remplacement qui nécessite généralement plusieurs jours d'immobilisation des zones concernées, une intervention de réparation peut souvent être réalisée en quelques heures, minimisant ainsi l'impact sur les activités quotidiennes de l'entrepôt.
Cette continuité opérationnelle représente un avantage majeur pour les entreprises fonctionnant en flux tendu ou disposant d'un espace de stockage limité. Elle permet d'éviter les retards de livraison, les ruptures de stock ou encore la désorganisation temporaire des flux logistiques, autant de conséquences potentiellement coûteuses d'une interruption prolongée de l'activité.
Durabilité et respect de l'environnement
Dans un contexte où les préoccupations environnementales prennent une importance croissante, la réparation des racks de stockage s'inscrit parfaitement dans une démarche de développement durable. En prolongeant la durée de vie des équipements existants, cette approche permet de réduire significativement la consommation de ressources et la production de déchets.
Selon une étude réalisée par Ecotica France et citée par ROS France, la réparation d'un montant d'échelle permet d'économiser jusqu'à 50% d'émissions de CO2 par rapport à son remplacement. Cette réduction s'explique principalement par l'économie de matières premières et d'énergie nécessaires à la fabrication, au transport et à l'installation de nouveaux composants.
Par ailleurs, la réparation génère considérablement moins de déchets métalliques que le remplacement. Bien que l'acier soit recyclable, le processus de recyclage lui-même consomme de l'énergie et génère des émissions. En évitant le remplacement systématique des composants endommagés, la réparation contribue donc à minimiser l'empreinte environnementale globale des activités logistiques.
Cette dimension écologique peut également s'intégrer dans la politique de responsabilité sociétale des entreprises (RSE), de plus en plus valorisée par les clients, les investisseurs et les autorités. En optant pour la réparation plutôt que le remplacement, les entreprises démontrent concrètement leur engagement en faveur d'une gestion plus durable de leurs ressources.
Enfin, certaines entreprises spécialisées dans la réparation, comme ROS France, proposent des solutions innovantes qui vont au-delà de la simple restauration des composants endommagés. Par exemple, l'installation de protections préventives sur les zones vulnérables permet de réduire la fréquence des dommages futurs, s'inscrivant ainsi dans une logique d'économie circulaire et de prolongation maximale de la durée de vie des équipements.
La réparation des racks de stockage représente donc une solution particulièrement avantageuse, combinant bénéfices économiques, opérationnels et environnementaux. Toutefois, dans certaines situations, une approche plus préventive peut s'avérer pertinente pour éviter l'apparition de dommages. C'est précisément l'objet du renforcement des racks, que nous allons explorer dans le chapitre suivant.
"L'inspection régulière des racks de stockage n'est pas une simple obligation réglementaire, c'est un investissement dans la sécurité et la pérennité des installations. Nos statistiques montrent qu'un programme d'inspection structuré permet de réduire de plus de 60% les incidents graves liés aux défaillances de rayonnages."
4. Le renforcement des racks : prévention et optimisation
Dans la gestion des infrastructures de stockage, la prévention des dommages s'avère aussi importante que leur réparation. Le renforcement des racks de stockage constitue une approche proactive qui vise à anticiper les problèmes avant qu'ils ne surviennent. Cette stratégie, complémentaire à la réparation, permet non seulement de prolonger la durée de vie des installations, mais également d'optimiser leur fonctionnement au quotidien. Toutefois, le renforcement ne se limite pas à une simple consolidation structurelle ; il s'agit d'une démarche globale qui intègre différentes techniques et solutions adaptées aux besoins spécifiques de chaque entrepôt.
Définition et objectifs du renforcement des racks
Le renforcement des racks de stockage peut être défini comme l'ensemble des mesures visant à augmenter la résistance des structures face aux contraintes quotidiennes, sans nécessairement intervenir sur des éléments déjà endommagés. Contrairement à la réparation, qui répond à un problème existant, le renforcement s'inscrit dans une logique préventive et anticipative.
Les objectifs du renforcement sont multiples. En premier lieu, il s'agit d'accroître la durabilité des installations en limitant les risques de déformation ou de rupture des composants. Cette amélioration de la résistance structurelle permet de réduire significativement la fréquence des interventions correctives, générant ainsi des économies substantielles à long terme.
Par ailleurs, le renforcement peut également viser à adapter les capacités des rayonnages à l'évolution des besoins logistiques. En effet, face à l'augmentation des charges ou à la modification des types de produits stockés, il peut s'avérer nécessaire de consolider les structures existantes plutôt que de procéder à leur remplacement complet.
Enfin, le renforcement contribue à améliorer la sécurité globale de l'entrepôt en réduisant les risques d'accidents liés à la défaillance des structures de stockage. Cette dimension sécuritaire est particulièrement importante dans un contexte où les exigences réglementaires et normatives se renforcent continuellement.
Différentes méthodes de renforcement
Les techniques de renforcement des racks de stockage sont nombreuses et variées, chacune répondant à des problématiques spécifiques. Parmi les solutions les plus couramment mises en œuvre, les protections d'échelles occupent une place prépondérante.
Ces dispositifs, généralement fabriqués en acier ou en matériaux composites, sont installés à la base des montants d'échelles, zones particulièrement exposées aux chocs des chariots élévateurs. Leur conception permet d'absorber l'énergie des impacts et de la dissiper, préservant ainsi l'intégrité structurelle des montants. Ces protections existent en différentes formes et tailles, adaptées aux configurations spécifiques des rayonnages : protections en L pour les montants d'angle, protections en U pour les montants intermédiaires, ou encore protections circulaires pour les poteaux isolés.
Les renforts de montants constituent une autre approche du renforcement. Il s'agit d'éléments métalliques fixés directement sur les montants existants, augmentant ainsi leur section et, par conséquent, leur résistance mécanique. Cette solution est particulièrement adaptée aux zones soumises à des charges importantes ou aux installations anciennes présentant des signes de fatigue matérielle.
Les butées de palettes représentent également un élément important du dispositif de renforcement. Placées à l'arrière des emplacements de stockage, elles empêchent les palettes de heurter directement les montants lors de leur mise en place. Ce système simple mais efficace permet de réduire considérablement les risques de dommages causés par des manœuvres imprécises.
Les grilles anti-chute, quant à elles, ne renforcent pas directement la structure des rayonnages, mais contribuent à la sécurité globale en empêchant la chute accidentelle de marchandises. Installées à l'arrière des travées, elles constituent une barrière physique qui limite les risques pour le personnel circulant dans les allées adjacentes.
Enfin, les systèmes de guidage au sol, tels que les rails ou les butées pour chariots élévateurs, participent indirectement au renforcement des installations en réduisant les risques de collision. En contraignant les trajectoires des engins de manutention, ces dispositifs minimisent les erreurs humaines et protègent ainsi les structures de stockage.
Situations où le renforcement est recommandé
Le renforcement des racks de stockage s'avère particulièrement pertinent dans plusieurs contextes spécifiques. Tout d'abord, dans les zones à fort trafic d'engins de manutention, où la probabilité de chocs est élevée, l'installation préventive de protections peut considérablement réduire la fréquence des dommages et, par conséquent, les coûts de maintenance associés.
De même, les emplacements accueillant des charges particulièrement lourdes ou des produits de grande valeur bénéficient grandement d'un renforcement adapté. Dans ces situations, la défaillance d'un élément structurel pourrait entraîner non seulement des dégâts matériels conséquents, mais également des pertes financières importantes liées à la détérioration des marchandises stockées.
Les entrepôts soumis à des contraintes environnementales spécifiques, tels que les chambres froides ou les zones à forte humidité, constituent également des candidats privilégiés pour le renforcement. En effet, ces conditions peuvent accélérer la dégradation des matériaux et fragiliser progressivement les structures.
Par ailleurs, lors de la réaffectation d'un espace de stockage à de nouveaux types de produits, notamment plus lourds ou plus volumineux que les précédents, le renforcement peut s'imposer comme une alternative économique au remplacement complet des installations. Cette approche permet d'adapter les infrastructures existantes aux nouvelles exigences opérationnelles, tout en limitant les investissements nécessaires.
Enfin, à la suite d'une réparation, le renforcement des zones adjacentes peut s'avérer judicieux pour prévenir la propagation des dommages. Cette démarche s'inscrit dans une logique de maintenance préventive qui vise à traiter non seulement les symptômes (les dégâts visibles), mais également leurs causes potentielles.
Quels sont les avantages du renforcement des racks de stockage ?
Loin d'être concurrentes, les approches de réparation et de renforcement se révèlent profondément complémentaires dans une stratégie globale de gestion des infrastructures de stockage. Cette synergie s'exprime à plusieurs niveaux et offre une réponse complète aux problématiques de maintenance des racks.
En premier lieu, la combinaison de ces deux approches permet d'adopter une vision à la fois corrective et préventive. La réparation traite les dommages existants, tandis que le renforcement anticipe les problèmes futurs, créant ainsi un cercle vertueux qui optimise la durée de vie des installations.
Par ailleurs, certaines solutions de réparation, comme celles proposées par ROS France, intègrent déjà une dimension de renforcement. En effet, les kits de réparation DAMO PRO, par exemple, ne se contentent pas de restaurer la géométrie d'origine des montants endommagés, mais les rendent également plus résistants aux impacts futurs. Cette double fonction illustre parfaitement la convergence naturelle entre réparation et renforcement.
De plus, l'analyse des causes de dommages, réalisée lors des interventions de réparation, fournit des informations précieuses pour orienter les stratégies de renforcement. En identifiant les zones particulièrement vulnérables ou fréquemment endommagées, il devient possible de déployer des solutions préventives ciblées et donc plus efficientes.
Sur le plan économique, cette complémentarité se traduit par une optimisation des investissements. En effet, la combinaison judicieuse de réparations ponctuelles et de renforcements stratégiques permet de maximiser le retour sur investissement des dépenses de maintenance, tout en minimisant les risques d'interruption opérationnelle.
Enfin, d'un point de vue organisationnel, l'intégration des activités de réparation et de renforcement facilite la gestion globale de la maintenance. Plutôt que de traiter ces aspects séparément, avec des interlocuteurs et des processus distincts, une approche unifiée simplifie la planification des interventions et améliore la cohérence des actions entreprises.
Des prestataires comme ROS France l'ont bien compris et proposent désormais des services intégrés couvrant l'ensemble du spectre, depuis l'inspection jusqu'au renforcement préventif, en passant par la réparation des éléments endommagés. Cette vision holistique de la maintenance des racks de stockage répond parfaitement aux attentes des gestionnaires d'entrepôts soucieux d'optimiser leurs infrastructures tout en maîtrisant leurs coûts.
Le renforcement des racks constitue donc un complément idéal à la réparation, permettant d'inscrire la gestion des infrastructures de stockage dans une démarche proactive et durable. Toutefois, malgré les avantages indéniables de ces approches, certaines situations peuvent nécessiter une solution plus radicale. Mais quand faut-il envisager le remplacement complet d'un rack plutôt que sa réparation ou son renforcement ? Le chapitre suivant explorera les circonstances qui justifient cette option et les facteurs à prendre en compte dans cette décision.
"Dans notre analyse du cycle de vie des équipements logistiques, nous avons constaté que la réparation d'un rack de stockage permet d'économiser en moyenne 120 kg d'équivalent CO2 par montant par rapport au remplacement. À l'échelle d'un grand entrepôt, l'impact environnemental est significatif."
5. Le remplacement des racks : quand est-ce nécessaire ?
Malgré les avantages indéniables de la réparation et du renforcement des racks de stockage, certaines situations exigent une solution plus radicale : le remplacement complet. Cette option, souvent perçue comme un dernier recours en raison de son coût élevé et des perturbations opérationnelles qu'elle engendre, s'avère parfois incontournable pour garantir la sécurité des installations et la continuité des activités logistiques. Comprendre les circonstances qui justifient le remplacement et maîtriser les contraintes associées permet aux gestionnaires d'entrepôts de prendre des décisions éclairées face à des rayonnages endommagés.
Cas où le remplacement est inévitable
Certains dommages, par leur nature ou leur étendue, rendent la réparation techniquement impossible ou économiquement injustifiée. C'est notamment le cas des déformations structurelles majeures, qui affectent profondément l'intégrité des composants. Lorsqu'un montant d'échelle présente une torsion importante ou une déformation complexe, les techniques de réparation conventionnelles peuvent s'avérer insuffisantes pour restaurer ses propriétés mécaniques d'origine.
De même, les dommages multiples concentrés sur une même zone fragilisent considérablement la structure et compliquent les interventions de réparation. Comme le souligne la certification VERITAS obtenue par ROS France, la réparation est recommandée à condition de "se limiter à 2 réparations au même endroit et à moins de 50 cm du choc initial". Au-delà de ces limites, le remplacement devient généralement la solution la plus appropriée pour garantir la sécurité des installations.
Les dommages causés par un incendie ou une inondation constituent également des cas typiques où le remplacement s'impose. En effet, l'exposition à des températures extrêmes ou à une humidité prolongée peut altérer les propriétés métallurgiques de l'acier, créant des faiblesses invisibles mais potentiellement dangereuses. Dans ces situations, même si les déformations visibles semblent limitées, le remplacement préventif des éléments exposés est souvent recommandé par les experts.
L'obsolescence technique représente une autre raison majeure de remplacement. Avec l'évolution des normes de sécurité et des besoins logistiques, certaines installations anciennes ne répondent plus aux exigences actuelles, malgré un état apparent satisfaisant. Dans ce contexte, le remplacement permet non seulement de résoudre les problèmes de conformité, mais également d'optimiser les performances globales du système de stockage en intégrant les innovations technologiques les plus récentes.
Enfin, les modifications significatives des besoins de stockage, comme l'augmentation substantielle des charges ou le changement radical du type de produits entreposés, peuvent nécessiter le remplacement des structures existantes par des équipements mieux adaptés aux nouvelles contraintes. Cette approche, bien que coûteuse à court terme, garantit une adéquation optimale entre les infrastructures et les exigences opérationnelles.
Processus de remplacement et contraintes associées
Le remplacement d'un rack de stockage, qu'il soit partiel ou complet, constitue une opération complexe qui doit être soigneusement planifiée pour minimiser les perturbations opérationnelles. Le processus commence généralement par une phase préparatoire comprenant l'évaluation détaillée des besoins, la sélection des nouveaux équipements et l'élaboration d'un calendrier d'intervention tenant compte des contraintes spécifiques de l'entrepôt.
Une fois cette planification établie, la première étape concrète consiste à décharger entièrement les zones concernées. Cette opération, apparemment simple, peut s'avérer particulièrement délicate dans les entrepôts à fort taux de remplissage, où l'espace disponible pour le stockage temporaire est limité. Elle nécessite souvent une réorganisation temporaire des flux logistiques et peut entraîner une réduction momentanée de la capacité opérationnelle.
Le démontage des structures existantes représente l'étape suivante. Cette phase requiert une expertise technique spécifique pour éviter tout risque d'effondrement ou d'accident. Les éléments démontés doivent ensuite être évacués, ce qui implique une logistique particulière, notamment pour les composants volumineux ou lourds. La gestion des déchets métalliques générés doit également respecter les réglementations environnementales en vigueur.
L'installation des nouveaux rayonnages constitue la phase centrale du processus. Elle débute généralement par la mise en place des ancrages au sol, suivie du montage des échelles et de l'installation des lisses. Cette étape cruciale doit être réalisée avec une précision absolue, car tout défaut d'alignement ou de niveau peut compromettre la stabilité de l'ensemble de la structure. Des contrôles rigoureux sont donc effectués tout au long du montage pour garantir la conformité aux spécifications techniques.
Enfin, avant la remise en service, une inspection finale est réalisée pour vérifier la conformité de l'installation aux normes en vigueur et aux exigences spécifiques du client. Cette validation, souvent effectuée par un organisme indépendant, conditionne l'autorisation d'utilisation des nouveaux équipements.
Il convient de souligner que ce processus s'étend généralement sur plusieurs jours, voire plusieurs semaines pour les installations importantes. Cette durée, bien supérieure à celle d'une intervention de réparation, constitue l'une des principales contraintes du remplacement, particulièrement dans les environnements logistiques fonctionnant en flux tendu.
Coûts directs et indirects du remplacement
L'évaluation complète du coût d'un remplacement de racks ne peut se limiter au simple prix d'achat des nouveaux équipements. Elle doit intégrer l'ensemble des dépenses directes et indirectes générées par cette opération.
Les coûts directs comprennent principalement l'acquisition des nouveaux rayonnages, les frais de démontage des structures existantes, les coûts de main-d'œuvre pour l'installation, ainsi que les dépenses liées à l'évacuation et au recyclage des anciens équipements. À ces éléments s'ajoutent les frais d'inspection et de certification, indispensables pour garantir la conformité des nouvelles installations.
Selon les données du secteur, le coût d'acquisition d'un rack à palettes neuf varie considérablement en fonction de sa capacité de charge, de sa hauteur et des options spécifiques requises. Pour une installation standard, il faut généralement compter entre 100 et 300 euros par emplacement palette, auxquels s'ajoutent les frais d'installation, estimés entre 20% et 30% du prix d'achat. Le démontage et l'évacuation des anciennes structures représentent quant à eux environ 15% à 20% du coût total.
Toutefois, les coûts indirects, souvent sous-estimés dans les évaluations initiales, peuvent représenter une part significative du budget global. Parmi ces coûts figurent les pertes de productivité liées à l'immobilisation des zones concernées, les dépenses supplémentaires pour le stockage temporaire des marchandises, ainsi que les éventuelles heures supplémentaires nécessaires pour maintenir le niveau d'activité pendant les travaux.
L'Assurance Maladie souligne également que les accidents liés aux rayonnages défectueux peuvent entraîner des conséquences graves pour les salariés. Au-delà des blessures potentielles, ces incidents peuvent générer des arrêts de travail prolongés et des séquelles permanentes. Pour l'entreprise, les répercussions se traduisent par des coûts directs (indemnisations, augmentation des cotisations AT/MP) et indirects (remplacement du personnel, désorganisation de la production).
Par ailleurs, le remplacement peut également engendrer des coûts cachés liés à la réorganisation des flux logistiques, à la mise à jour des systèmes informatiques de gestion d'entrepôt, ou encore à la formation du personnel aux spécificités des nouveaux équipements. Ces aspects, bien que difficiles à quantifier précisément, doivent être pris en compte dans l'analyse économique globale.
Face à ces coûts substantiels, la réparation apparaît souvent comme une alternative économiquement avantageuse. Comme mentionné précédemment, ROS France estime que "la réparation des montants endommagés assure une économie de 80% du coût de leur remplacement". Cette différence significative s'explique non seulement par les économies réalisées sur les matériaux et la main-d'œuvre, mais également par la réduction drastique des perturbations opérationnelles et des coûts indirects associés.
Comparaison détaillée : remplacement vs réparation
Pour éclairer la décision entre remplacement et réparation, une analyse comparative approfondie s'impose, prenant en compte non seulement les aspects financiers, mais également les dimensions opérationnelles, temporelles et environnementales.
Sur le plan financier, comme évoqué précédemment, la réparation présente un avantage considérable, avec une économie pouvant atteindre 80% par rapport au remplacement. Cet écart s'explique par des coûts matériels réduits, une main-d'œuvre moins importante et des perturbations opérationnelles limitées. Toutefois, cette comparaison doit être nuancée en fonction de l'étendue des dommages et de l'âge des installations. Pour des structures anciennes présentant des signes d'usure généralisée, le remplacement peut s'avérer plus économique à long terme, en évitant des interventions de réparation répétées.
En termes de délais, la différence est également significative. Alors qu'une réparation selon le procédé ROS peut généralement être réalisée en quelques heures, un remplacement complet nécessite souvent plusieurs jours, voire plusieurs semaines en fonction de la disponibilité des pièces et de la complexité de l'installation. Ce facteur temps peut s'avérer déterminant dans les environnements logistiques à forte activité, où chaque jour d'immobilisation représente un manque à gagner considérable.
L'impact sur les opérations quotidiennes constitue un autre critère de comparaison essentiel. La réparation, particulièrement lorsqu'elle peut être effectuée sans déchargement comme le propose ROS France, perturbe minimalement les activités de l'entrepôt. À l'inverse, le remplacement implique nécessairement un déchargement complet des zones concernées, une réorganisation temporaire des flux et potentiellement une réduction de la capacité opérationnelle pendant toute la durée des travaux.
Sur le plan environnemental, la réparation s'inscrit davantage dans une logique d'économie circulaire en prolongeant la durée de vie des équipements existants. Selon le rapport d'Ecotica France cité par ROS France, elle permet d'économiser jusqu'à 50% de CO2 par rapport au remplacement. Cette dimension écologique prend une importance croissante dans les décisions d'entreprise, notamment dans un contexte de renforcement des politiques de responsabilité environnementale.
Enfin, la comparaison doit également intégrer des aspects qualitatifs tels que la garantie offerte, la durabilité de la solution ou encore la conformité aux normes en vigueur. Sur ce point, les certifications obtenues par des entreprises comme ROS France (DEKRA, Bureau Veritas) offrent des garanties comparables à celles des fabricants de rayonnages neufs, levant ainsi les réticences potentielles quant à la fiabilité des réparations.
Cette analyse comparative met en évidence les avantages substantiels de la réparation dans de nombreuses situations. Toutefois, elle souligne également l'existence de cas spécifiques où le remplacement demeure la solution la plus appropriée. La décision finale doit donc s'appuyer sur une évaluation rigoureuse de chaque situation particulière, prenant en compte l'ensemble des facteurs évoqués.
Comment prendre la décision la plus adaptée à votre situation spécifique ? Quels critères privilégier face à un rack endommagé ? Le chapitre suivant proposera un guide pratique pour orienter ce choix crucial entre réparation, renforcement et remplacement, en fonction des caractéristiques propres à chaque installation.
"L'avenir des racks de stockage réside dans leur intégration à l'écosystème digital de l'entrepôt. Les rayonnages connectés, capables de communiquer leur état en temps réel, transformeront fondamentalement notre approche de la maintenance, passant d'un modèle réactif à une gestion véritablement prédictive."
6. Guide pratique : choisir entre réparation, renforcement ou remplacement
Face à un rack de stockage endommagé, la décision entre réparation, renforcement ou remplacement peut s'avérer complexe. Cette décision, loin d'être anodine, engage la sécurité des installations, la continuité des opérations logistiques et les finances de l'entreprise. Pour faciliter ce choix crucial, il convient d'adopter une approche méthodique, prenant en compte l'ensemble des facteurs pertinents. Ce guide pratique propose une démarche structurée pour déterminer la solution la plus adaptée à chaque situation spécifique.
Critères de décision
La nature et l'étendue des dommages constituent naturellement le premier critère à considérer. Comme évoqué précédemment, la classification établie par la norme NF EN 15635 offre un cadre de référence précieux pour évaluer la gravité des détériorations. Les dommages de niveau vert, correspondant à des déformations légères, se prêtent généralement bien à la réparation. Les dommages de niveau jaune nécessitent une intervention rapide, mais peuvent souvent être traités par des techniques de réparation avancées comme celles proposées par ROS France. En revanche, les dommages de niveau rouge, particulièrement sévères, peuvent dans certains cas justifier un remplacement, notamment lorsqu'ils affectent profondément l'intégrité structurelle des composants.
L'âge et l'état général des installations représentent également des facteurs déterminants. Pour des rayonnages relativement récents et en bon état général, la réparation ou le renforcement constituent généralement les options les plus pertinentes. En revanche, pour des structures anciennes présentant des signes d'usure généralisée ou ne répondant plus aux normes actuelles, le remplacement peut s'avérer plus judicieux à long terme, malgré un investissement initial plus important.
Les contraintes opérationnelles de l'entrepôt doivent également être prises en compte. Dans les environnements fonctionnant en flux tendu, où toute interruption d'activité engendre des coûts significatifs, la réparation sans déchargement présente un avantage considérable. À l'inverse, si l'activité connaît des périodes creuses permettant de libérer temporairement certaines zones, le remplacement peut être envisagé avec un impact opérationnel limité.
La fréquence des dommages sur une même zone constitue un indicateur précieux pour orienter la décision. Des détériorations récurrentes suggèrent généralement un problème structurel ou organisationnel plus profond, qui ne sera pas résolu par de simples réparations successives. Dans ces situations, le renforcement préventif ou, dans les cas extrêmes, le remplacement par des équipements plus adaptés aux contraintes spécifiques de la zone peut s'avérer nécessaire.
Le budget disponible et l'horizon d'investissement représentent évidemment des facteurs incontournables. Si la réparation offre généralement une solution plus économique à court terme, le remplacement peut parfois s'avérer plus avantageux dans une perspective de long terme, notamment en réduisant les coûts de maintenance futurs ou en permettant une optimisation de l'espace de stockage.
Enfin, les objectifs stratégiques de l'entreprise en matière de développement durable ne doivent pas être négligés. Dans un contexte où la responsabilité environnementale prend une importance croissante, la réparation, qui permet de réduire significativement l'empreinte carbone par rapport au remplacement, peut s'aligner davantage avec les politiques RSE de l'organisation.
Comment choisir entre réparation, renforcement ou remplacement des racks de stockage ?
Pour faciliter la prise de décision, un arbre décisionnel structuré peut s'avérer particulièrement utile. Cet outil méthodologique permet d'organiser logiquement les différents critères évoqués précédemment et de les articuler dans un processus de décision séquentiel.
La première étape consiste à évaluer la gravité des dommages selon la classification de la norme NF EN 15635 :
- Pour les dommages de niveau vert (déformation légère) : la réparation est généralement recommandée, éventuellement complétée par un renforcement préventif des zones adjacentes.
- Pour les dommages de niveau jaune (état dangereux) : une analyse plus approfondie s'impose, prenant en compte l'étendue exacte des dégâts, leur localisation et leur impact sur la stabilité globale de la structure.
- Pour les dommages de niveau rouge (danger imminent) : le déchargement immédiat est impératif, suivi d'une évaluation détaillée pour déterminer si la réparation est techniquement possible ou si le remplacement s'impose.
Si la réparation semble techniquement envisageable, l'étape suivante consiste à évaluer sa pertinence économique. Cette analyse doit intégrer non seulement les coûts directs de l'intervention, mais également les coûts indirects liés aux perturbations opérationnelles, ainsi que les coûts futurs de maintenance. La comparaison avec le coût total d'un remplacement, également calculé en intégrant l'ensemble des dépenses directes et indirectes, permet alors de déterminer l'option la plus avantageuse financièrement.
Parallèlement, l'analyse des causes des dommages peut orienter vers la nécessité d'un renforcement complémentaire. Si les détériorations résultent de chocs répétés dans une zone spécifique, l'installation de protections adaptées peut s'avérer judicieuse, quelle que soit l'option retenue (réparation ou remplacement). De même, si les dommages sont liés à une surcharge chronique, un renforcement structurel ou une révision des pratiques de stockage peut être nécessaire.
Enfin, l'évaluation des contraintes opérationnelles spécifiques de l'entrepôt permet d'affiner la décision. La disponibilité d'espaces de stockage temporaires, les périodes d'activité réduite permettant des interventions plus importantes, ou encore les projets d'évolution à moyen terme des activités logistiques sont autant de facteurs qui peuvent influencer le choix final.
Cet arbre décisionnel, bien que fournissant un cadre méthodologique précieux, ne remplace pas l'expertise de professionnels qualifiés. Une évaluation sur site par des spécialistes des structures de stockage reste indispensable pour garantir la pertinence de la décision et la sécurité des installations.
Importance de faire appel à des professionnels certifiés
Quelle que soit l'option retenue – réparation, renforcement ou remplacement – l'intervention de professionnels certifiés s'avère essentielle pour garantir la qualité et la sécurité des travaux réalisés. Cette exigence, loin d'être une simple précaution, répond à des impératifs techniques, réglementaires et assurantiels.
Sur le plan technique, la complexité des structures de rayonnages industriels et les contraintes mécaniques auxquelles elles sont soumises nécessitent une expertise spécifique. Les professionnels certifiés disposent non seulement des compétences théoriques nécessaires, mais également de l'expérience pratique et des outils adaptés pour réaliser des interventions conformes aux standards les plus exigeants.
Du point de vue réglementaire, le recours à des intervenants qualifiés s'inscrit dans le cadre des obligations générales de sécurité imposées aux employeurs par le Code du travail. En cas d'accident lié à une défaillance des équipements, la responsabilité de l'entreprise peut être engagée, particulièrement si les interventions de maintenance n'ont pas été réalisées par des professionnels dûment qualifiés.
Par ailleurs, les assureurs exigent généralement que les interventions sur les structures de stockage soient effectuées par des entreprises certifiées. Le non-respect de cette exigence peut entraîner des difficultés en cas de sinistre, avec un risque de non-prise en charge des dommages par l'assurance.
Dans le domaine de la réparation, des entreprises comme ROS France, bénéficiant de certifications reconnues (DEKRA, Bureau Veritas), offrent des garanties essentielles quant à la qualité et à la conformité des interventions. Ces certifications, obtenues après des tests rigoureux et des audits réguliers, attestent que les méthodes employées permettent de restaurer les propriétés mécaniques d'origine des structures, conformément aux exigences normatives.
Pour le renforcement, le recours à des spécialistes permet de bénéficier de solutions adaptées aux problématiques spécifiques de chaque installation. Ces professionnels peuvent non seulement recommander les dispositifs les plus pertinents, mais également garantir leur installation correcte, condition indispensable à leur efficacité.
Enfin, en cas de remplacement, l'intervention d'équipes spécialisées assure le respect des spécifications techniques du fabricant et des normes en vigueur. De la préparation du sol à l'installation des lisses, en passant par le montage des échelles, chaque étape requiert une précision et un savoir-faire que seuls des professionnels expérimentés peuvent garantir.
Témoignages et études de cas
Pour illustrer concrètement les différentes approches évoquées précédemment, examinons quelques cas réels d'interventions sur des racks de stockage endommagés. Ces exemples, issus de différents secteurs d'activité, mettent en lumière la diversité des situations rencontrées et des solutions mises en œuvre.
Dans un entrepôt logistique de la région lyonnaise, spécialisé dans la distribution de produits alimentaires, plusieurs montants d'échelles présentaient des déformations de niveau jaune suite à des chocs de chariots élévateurs. La contrainte majeure résidait dans l'impossibilité d'interrompre l'activité, même temporairement, en raison des engagements contractuels avec les clients. La solution retenue a été une réparation sans déchargement selon le procédé ROS, complétée par l'installation de protections d'échelles pour prévenir de futurs dommages. Cette approche combinée a permis de restaurer la sécurité des installations tout en maintenant l'activité opérationnelle, pour un coût représentant environ 25% de celui d'un remplacement équivalent.
Un autre cas intéressant concerne un centre de distribution de pièces automobiles en région parisienne. Les rayonnages, installés depuis plus de 15 ans, présentaient des signes d'usure généralisée et ne répondaient plus aux normes actuelles en termes de capacité de charge. Par ailleurs, l'évolution des références stockées nécessitait une reconfiguration des niveaux. Dans ce contexte, malgré le coût initial plus élevé, le remplacement complet s'est imposé comme la solution la plus pertinente. Planifiée pendant une période d'activité réduite, cette opération a permis non seulement de résoudre les problèmes de sécurité, mais également d'optimiser l'organisation du stockage, générant à terme des gains de productivité significatifs.
Dans une entreprise de l'industrie chimique, les racks situés dans une zone de stockage de produits corrosifs présentaient une dégradation accélérée due à l'environnement agressif. Plutôt qu'un remplacement fréquent, l'entreprise a opté pour une stratégie de renforcement préventif, avec l'application de revêtements protecteurs spécifiques et l'installation de composants en matériaux résistants à la corrosion. Cette approche proactive a permis de prolonger considérablement la durée de vie des installations tout en réduisant les coûts de maintenance à long terme.
Enfin, un fabricant de matériaux de construction a été confronté à un cas particulièrement complexe : suite à un léger affaissement du sol dans une partie de l'entrepôt, plusieurs travées de rayonnages présentaient des déformations structurelles. Après une analyse approfondie, une solution hybride a été mise en œuvre : remplacement des échelles les plus affectées, réparation des éléments présentant des dommages modérés, et renforcement général de la structure pour compenser les irrégularités du sol. Cette approche sur mesure, bien que techniquement complexe, a permis d'optimiser le rapport coût-efficacité de l'intervention.
Ces différents exemples illustrent l'importance d'une analyse au cas par cas, prenant en compte l'ensemble des facteurs spécifiques à chaque situation. Ils soulignent également la valeur ajoutée d'une expertise professionnelle pour identifier la solution la plus adaptée aux contraintes techniques, opérationnelles et financières de chaque entreprise.
Maintenant que nous avons exploré les différentes options curatives face à des racks endommagés, il convient de s'intéresser aux approches préventives permettant de limiter l'apparition de ces dommages. Comment prolonger la durée de vie de vos installations de stockage ? Quelles mesures mettre en place pour réduire les risques d'incidents ? Le chapitre suivant vous propose des stratégies concrètes pour optimiser la maintenance de vos racks et minimiser les interventions correctives.
7. Stratégies préventives pour prolonger la durée de vie des racks
Au-delà des approches curatives comme la réparation, le renforcement ou le remplacement, la mise en place de stratégies préventives s'avère essentielle pour optimiser la durée de vie des racks de stockage. Ces mesures proactives permettent non seulement de réduire la fréquence des dommages, mais également de minimiser les coûts de maintenance et d'améliorer la sécurité globale de l'entrepôt. Une approche préventive bien structurée repose sur plusieurs piliers complémentaires, depuis la formation du personnel jusqu'à l'inspection régulière des installations, en passant par l'installation de dispositifs de protection adaptés.
Formation des opérateurs de chariots élévateurs
Les chocs causés par les engins de manutention représentant l'une des principales causes de dommages sur les racks de stockage, la formation des caristes constitue un levier préventif majeur. Cette formation doit dépasser le simple apprentissage technique de la conduite pour intégrer une véritable sensibilisation aux enjeux de sécurité liés aux rayonnages.
Le programme de formation doit notamment aborder les techniques de manœuvre sécuritaires à proximité des structures de stockage, en insistant sur la précision des mouvements et le respect des distances de sécurité. Les opérateurs doivent être sensibilisés aux conséquences potentielles d'un impact, même apparemment mineur, sur l'intégrité structurelle des rayonnages.
Par ailleurs, la formation doit inclure un volet spécifique sur le chargement et le déchargement des palettes, opérations particulièrement délicates qui génèrent fréquemment des dommages. Les caristes doivent maîtriser les techniques permettant d'éviter tout contact entre les fourches du chariot et les lisses ou les montants des racks.
La connaissance des capacités de charge des rayonnages constitue également un aspect essentiel de cette formation. Les opérateurs doivent être en mesure d'identifier les situations de surcharge potentielle et de signaler tout problème observé lors de leurs activités quotidiennes.
Enfin, des sessions de recyclage régulières permettent de maintenir un niveau de vigilance élevé et d'intégrer les évolutions techniques ou organisationnelles. Ces formations continues peuvent s'appuyer sur des cas concrets rencontrés dans l'entrepôt, renforçant ainsi leur pertinence et leur impact sur les pratiques quotidiennes.
Installation de protections préventives
L'installation stratégique de dispositifs de protection constitue un complément indispensable à la formation du personnel. Ces équipements, spécifiquement conçus pour absorber les chocs et préserver l'intégrité des structures, offrent une barrière physique efficace contre les dommages accidentels.
Les protections d'échelles, généralement installées à la base des montants, représentent la solution la plus courante. Disponibles en différentes configurations (protections en L, en U, circulaires), elles sont adaptées aux spécificités de chaque installation. Ces dispositifs, fabriqués en acier ou en matériaux composites à haute résistance, absorbent l'énergie des impacts et la dissipent, évitant ainsi sa transmission directe aux composants structurels des rayonnages.
Les butées de palettes, positionnées à l'arrière des emplacements de stockage, empêchent les palettes de heurter directement les montants lors de leur mise en place. Cette solution simple mais efficace réduit considérablement les risques de dommages causés par des manœuvres imprécises ou des charges mal positionnées.
Les protections de lisses, moins répandues mais tout aussi utiles, préviennent les déformations causées par les fourches des chariots élévateurs lors des opérations de prise ou de dépose des palettes. Elles prolongent significativement la durée de vie de ces composants horizontaux essentiels à la stabilité des structures.
Les barrières de protection au sol, installées le long des allées de circulation, délimitent clairement les zones accessibles aux engins de manutention et créent une distance de sécurité avec les rayonnages. Particulièrement pertinentes dans les zones à fort trafic ou aux intersections, elles réduisent considérablement les risques de collision.
Enfin, les miroirs de sécurité, stratégiquement positionnés aux intersections d'allées ou dans les angles morts, améliorent la visibilité des caristes et réduisent les risques de manœuvres hasardeuses. Bien que moins directement protecteurs que les dispositifs physiques, ils contribuent significativement à la prévention des accidents.
L'installation de ces différentes protections doit s'inscrire dans une approche globale, tenant compte des spécificités de chaque zone de l'entrepôt, des flux de circulation et des types d'engins utilisés. Une cartographie des risques, identifiant les points particulièrement vulnérables, permet d'optimiser le déploiement de ces dispositifs et de maximiser leur efficacité préventive.
Comment prolonger la durée de vie des racks de stockage ?
La détection précoce des anomalies constitue un élément clé de toute stratégie préventive efficace. Un programme d'inspection structuré, conforme aux recommandations de la norme NF EN 15635, permet d'identifier et de traiter les problèmes avant qu'ils ne s'aggravent et ne compromettent la sécurité des installations.
Ce programme doit s'articuler autour de trois niveaux d'inspection complémentaires. L'inspection visuelle quotidienne, réalisée par les opérateurs dans le cadre de leurs activités habituelles, constitue la première ligne de défense. Bien que sommaire, ce contrôle régulier permet de détecter rapidement les anomalies évidentes, telles que les déformations importantes ou les éléments manquants. Pour être efficace, cette pratique doit être formalisée et intégrée aux procédures opérationnelles standard de l'entrepôt.
L'INRS (Institut National de Recherche et de Sécurité) recommande une inspection hebdomadaire, plus approfondie, généralement effectuée par un responsable d'entrepôt ou un chef d'équipe spécifiquement formé à cette tâche. Elle vise à identifier systématiquement les dommages de niveau vert ou jaune, afin de planifier les interventions nécessaires avant que la situation ne se dégrade davantage. Cette inspection doit suivre un protocole précis, couvrant l'ensemble des éléments structurels des rayonnages : montants, lisses, connecteurs, ancrages, etc.
Enfin, l'inspection annuelle, réalisée par un expert qualifié, permet une évaluation complète et détaillée de l'état des installations. Cette inspection, qui peut être confiée à un organisme externe comme DEKRA ou Bureau Veritas, donne lieu à un rapport détaillé identifiant les non-conformités et recommandant les actions correctives appropriées. Elle constitue également une occasion de vérifier la conformité des installations aux normes en vigueur, qui peuvent évoluer au fil du temps.
Pour faciliter ces inspections et assurer leur traçabilité, il est recommandé de mettre en place un système de documentation rigoureux. Des fiches d'inspection standardisées, des photographies des dommages identifiés, ainsi qu'un registre centralisant l'historique des contrôles et des interventions constituent des outils précieux pour une gestion efficace de la maintenance des racks.
L'utilisation de technologies modernes peut également optimiser ce processus d'inspection. Des applications mobiles dédiées permettent aux inspecteurs de saisir directement leurs observations sur le terrain, de les documenter par des photographies géolocalisées et de générer automatiquement des rapports structurés. Certaines solutions avancées intègrent même des fonctionnalités de réalité augmentée, facilitant la comparaison avec les inspections précédentes ou la visualisation des déformations par rapport à la géométrie théorique des structures.
Maintenance préventive vs corrective
L'arbitrage entre maintenance préventive et corrective constitue un enjeu stratégique pour les gestionnaires d'entrepôts. Si la maintenance corrective, qui consiste à intervenir uniquement lorsqu'un dommage est constaté, peut sembler plus économique à court terme, la maintenance préventive offre généralement un meilleur retour sur investissement dans une perspective de long terme.
La maintenance préventive, qui englobe l'ensemble des mesures visant à anticiper et prévenir les défaillances avant qu'elles ne surviennent, présente de nombreux avantages. Elle permet tout d'abord de réduire significativement la fréquence des interventions correctives, généralement plus coûteuses et plus perturbatrices pour l'activité opérationnelle. Par ailleurs, en limitant les dommages majeurs, elle prolonge la durée de vie globale des installations et retarde la nécessité d'investissements lourds de remplacement.
Sur le plan de la sécurité, la maintenance préventive offre un niveau de protection supérieur en réduisant les risques d'incidents graves liés à des défaillances structurelles. Cette dimension sécuritaire, au-delà de son importance intrinsèque pour la protection des personnes, présente également des avantages économiques indirects en limitant les risques d'accidents du travail, d'arrêts d'activité imposés par les autorités ou de litiges avec les assureurs.
Toutefois, la mise en place d'une stratégie de maintenance préventive efficace nécessite un investissement initial en termes de ressources humaines, de formation et d'équipements. Elle implique également une organisation rigoureuse et un suivi méthodique des interventions. Pour optimiser le rapport coût-bénéfice de cette approche, il convient d'adapter le niveau d'intensité de la maintenance préventive aux spécificités de chaque zone de l'entrepôt, en fonction des risques identifiés et des enjeux opérationnels.
Une approche équilibrée, combinant maintenance préventive ciblée et maintenance corrective réactive, permet généralement d'optimiser les ressources tout en garantissant un niveau de sécurité satisfaisant. Cette stratégie hybride s'appuie sur une analyse de risques détaillée, identifiant les zones critiques nécessitant une attention préventive particulière et celles où une approche plus réactive peut être acceptable.
Des outils d'aide à la décision, tels que l'analyse des modes de défaillance, de leurs effets et de leur criticité (AMDEC), peuvent faciliter cette priorisation en évaluant systématiquement les risques associés à chaque type de défaillance potentielle. Cette méthodologie structurée permet d'allouer les ressources de maintenance de manière optimale, en concentrant les efforts préventifs sur les éléments présentant les niveaux de criticité les plus élevés.
En définitive, une stratégie de maintenance efficace doit s'inscrire dans une démarche d'amélioration continue, s'adaptant à l'évolution des installations, des activités logistiques et des technologies disponibles. L'analyse régulière des données d'inspection et d'intervention permet d'affiner progressivement cette stratégie, en identifiant les tendances émergentes et en ajustant les protocoles en conséquence.
Les stratégies préventives constituent donc un levier essentiel pour optimiser la durée de vie des racks de stockage et garantir la sécurité des installations. Toutefois, le domaine de la maintenance des rayonnages connaît actuellement des évolutions technologiques majeures, ouvrant de nouvelles perspectives pour une gestion encore plus efficace et proactive. Quelles sont ces innovations et comment pourraient-elles transformer les pratiques actuelles ? C'est ce que nous allons explorer dans le chapitre suivant.
8. Innovations et tendances futures dans la gestion des racks de stockage
Le domaine de la gestion des racks de stockage connaît actuellement une véritable révolution technologique. Des innovations majeures émergent, transformant progressivement les approches traditionnelles de conception, d'utilisation et de maintenance des rayonnages industriels. Ces avancées, portées par la digitalisation croissante de la logistique et l'essor de l'Internet des Objets Industriel (IIoT), ouvrent des perspectives prometteuses pour une gestion plus efficace, plus sécurisée et plus durable des infrastructures de stockage. Découvrons les tendances les plus significatives qui façonneront l'avenir de ce secteur.
Nouvelles technologies de réparation et de renforcement
Les techniques de réparation et de renforcement des racks de stockage bénéficient d'innovations constantes, tant au niveau des matériaux utilisés que des méthodes d'intervention. L'émergence de composites à haute résistance, combinant légèreté et propriétés mécaniques exceptionnelles, permet désormais de concevoir des solutions de réparation plus performantes et plus durables que les approches traditionnelles basées uniquement sur l'acier.
Ces nouveaux matériaux, issus notamment de l'industrie aérospatiale, offrent des rapports résistance/poids particulièrement avantageux. Leur utilisation dans les kits de réparation permet non seulement de restaurer les propriétés mécaniques d'origine des structures endommagées, mais souvent de les améliorer, augmentant ainsi leur résistance aux chocs futurs. Par ailleurs, certains de ces matériaux présentent des propriétés anti-corrosion supérieures à celles de l'acier conventionnel, prolongeant significativement la durée de vie des composants réparés, particulièrement dans les environnements agressifs.
Au-delà des matériaux, les méthodes d'intervention évoluent également, avec le développement de techniques non invasives permettant des réparations encore plus rapides et moins perturbatrices pour l'activité opérationnelle. Des entreprises comme ROS France investissent continuellement dans la recherche et développement pour optimiser leurs procédés, réduisant ainsi les temps d'intervention tout en améliorant la qualité et la durabilité des réparations.
L'impression 3D fait également son apparition dans ce domaine, permettant la fabrication sur mesure de pièces de renforcement parfaitement adaptées aux spécificités de chaque installation. Cette technologie, encore émergente pour les applications structurelles, pourrait révolutionner l'approche de la réparation en permettant la production rapide de composants personnalisés, directement sur site, réduisant ainsi les délais d'intervention et les coûts logistiques.
Enfin, des revêtements intelligents, capables de changer de couleur en fonction des contraintes subies ou de s'auto-réparer en cas de dommages mineurs, sont actuellement en développement. Ces solutions, inspirées des matériaux biomimétiques, pourraient constituer une avancée majeure dans la prévention et la détection précoce des dommages sur les structures de stockage.
Systèmes de surveillance et de détection des dommages
La surveillance des racks de stockage connaît une transformation profonde avec l'intégration de technologies numériques avancées. Les systèmes traditionnels d'inspection visuelle, bien qu'essentiels, sont progressivement complétés par des solutions automatisées permettant une détection plus précoce et plus précise des anomalies.
Les capteurs connectés, installés à des points stratégiques des structures, permettent un monitoring continu des paramètres critiques tels que les déformations, les vibrations ou les charges appliquées. Ces dispositifs, de plus en plus miniaturisés et autonomes énergétiquement, transmettent en temps réel des données qui sont analysées par des algorithmes spécifiques pour détecter toute anomalie ou tendance préoccupante. Cette approche proactive permet d'identifier les problèmes potentiels avant qu'ils ne deviennent critiques, optimisant ainsi la planification des interventions de maintenance.
Les technologies d'imagerie avancée, comme la photogrammétrie ou la scannerisation laser 3D, révolutionnent également les méthodes d'inspection. Ces techniques permettent de créer des modèles numériques précis des installations, qui peuvent être comparés à la géométrie théorique ou aux relevés précédents pour identifier avec une précision millimétrique les déformations ou les déplacements. Certaines solutions intègrent même des drones autonomes équipés de caméras haute résolution, capables d'inspecter rapidement de vastes zones de stockage, y compris les niveaux les plus élevés, difficilement accessibles par les méthodes conventionnelles.
L'intelligence artificielle joue un rôle croissant dans l'interprétation des données issues de ces différents systèmes de surveillance. Des algorithmes d'apprentissage automatique, entraînés sur des bases de données d'incidents passés, peuvent identifier des patterns subtils annonciateurs de défaillances potentielles. Cette capacité prédictive permet d'intervenir de manière préventive, avant même que les seuils d'alerte traditionnels ne soient atteints.
Ces innovations en matière de surveillance s'inscrivent dans la tendance plus large de l'Internet des Objets Industriel (IIoT) et de l'Industrie 4.0. Elles contribuent à transformer la maintenance des racks de stockage, en la faisant évoluer d'une approche périodique ou réactive vers un modèle véritablement prédictif, optimisant ainsi les ressources tout en maximisant la sécurité.
Les racks de stockage intelligents : quelle révolution pour la logistique ?
Au-delà des systèmes de surveillance externes, l'intelligence s'intègre progressivement aux rayonnages eux-mêmes, donnant naissance au concept de "racks intelligents". Ces structures de nouvelle génération incorporent dès leur conception des fonctionnalités avancées qui révolutionnent leur utilisation et leur maintenance.
L'intégration de capteurs directement dans les composants structurels des rayonnages permet une surveillance en temps réel de leur état. Ces capteurs, conçus pour résister aux conditions d'utilisation intensive des entrepôts, peuvent mesurer en continu les charges appliquées, détecter les impacts et évaluer l'intégrité structurelle. Certains modèles avancés intègrent même des systèmes d'alerte visuelle immédiate, comme des indicateurs LED qui changent de couleur en fonction de l'état du rack, offrant ainsi une information instantanée aux opérateurs.
La connectivité constitue une autre dimension essentielle de ces racks intelligents. Grâce à des technologies de communication sans fil à faible consommation énergétique, comme le Bluetooth Low Energy (BLE) ou le LoRaWAN, les données collectées par les capteurs sont transmises à des systèmes centralisés de gestion. Cette connectivité permet non seulement le monitoring à distance, mais également l'intégration avec d'autres systèmes de l'entrepôt, comme les logiciels de gestion d'entrepôt (WMS) ou les plateformes de maintenance.
Certains racks intelligents intègrent également des fonctionnalités d'identification automatique des marchandises stockées. Des technologies comme la RFID (Radio Frequency Identification) ou les codes QR dynamiques permettent de suivre précisément l'emplacement et les mouvements des produits, optimisant ainsi la gestion des stocks et réduisant les erreurs de picking. Ces systèmes peuvent également contribuer à une meilleure répartition des charges, en guidant les opérateurs vers les emplacements les plus appropriés en fonction du poids et des caractéristiques des palettes.
L'autonomie énergétique représente un défi majeur pour ces rayonnages connectés. Des solutions innovantes émergent, comme les capteurs auto-alimentés par récupération d'énergie (energy harvesting), capables de convertir les vibrations, les variations de température ou même la lumière ambiante en électricité. Ces technologies permettent de déployer des réseaux de capteurs sans contrainte de câblage ou de remplacement de batteries, facilitant ainsi leur adoption à grande échelle.
Ces racks intelligents s'inscrivent dans la vision plus large de l'entrepôt connecté, où l'ensemble des équipements et des processus sont intégrés dans un écosystème digital cohérent. Cette convergence technologique ouvre la voie à des optimisations significatives en termes d'efficacité opérationnelle, de sécurité et de durabilité des infrastructures logistiques.
Évolution des normes et réglementations
Le cadre normatif et réglementaire encadrant les racks de stockage connaît également des évolutions significatives, reflétant à la fois les avancées technologiques et une exigence croissante en matière de sécurité. Ces évolutions impactent directement les pratiques de conception, d'installation et de maintenance des rayonnages industriels.
La série de normes européennes EN 15635, qui définit les principes d'utilisation et de maintenance des systèmes de stockage statiques en acier, fait l'objet de révisions régulières pour intégrer les retours d'expérience du terrain et les innovations technologiques. Les versions récentes accordent une attention particulière aux méthodes d'inspection assistées par des technologies numériques, reconnaissant leur potentiel pour améliorer la détection précoce des anomalies.
Par ailleurs, de nouvelles normes émergent spécifiquement pour encadrer les solutions de réparation et de renforcement. Ces référentiels, développés en collaboration avec les acteurs du secteur, visent à garantir l'efficacité et la sécurité des interventions, tout en facilitant leur validation par les organismes de certification et les assureurs. Des entreprises comme ROS France participent activement à ces travaux de normalisation, partageant leur expertise pour contribuer à l'élaboration de standards exigeants et pertinents.
Sur le plan réglementaire, on observe un renforcement des exigences en matière de documentation et de traçabilité. Les gestionnaires d'entrepôts sont de plus en plus tenus de maintenir un historique détaillé des inspections, des interventions et des modifications apportées aux structures de stockage. Cette exigence de traçabilité favorise l'adoption de solutions digitales de gestion de la maintenance, permettant une centralisation et une accessibilité accrues des informations critiques.
La dimension environnementale prend également une importance croissante dans l'évolution des normes. Les principes de l'économie circulaire et de l'écoconception s'intègrent progressivement dans les référentiels, encourageant des approches favorisant la durabilité, la réparabilité et le recyclage des composants. Cette tendance renforce la pertinence des solutions de réparation et de renforcement, qui s'inscrivent naturellement dans une logique de prolongation de la durée de vie des équipements.
Enfin, l'approche réglementaire évolue vers une responsabilisation accrue des différents acteurs. Au-delà des exigences techniques spécifiques, les nouvelles normes mettent davantage l'accent sur les processus de gestion des risques, la formation du personnel et la documentation des contrôles effectués. Cette approche systémique vise à créer une véritable culture de la sécurité, où chaque intervenant, du fabricant à l'utilisateur final, assume pleinement ses responsabilités.
Pour les gestionnaires d'entrepôts, cette évolution constante des normes implique une veille réglementaire active et une capacité d'adaptation. Des entreprises spécialisées comme ROS France jouent un rôle crucial dans ce contexte, en proposant des solutions conformes aux standards les plus récents et en accompagnant leurs clients dans leur mise en conformité.
L'avenir des racks de stockage : perspectives et innovations
Les innovations et tendances futures dans la gestion des racks de stockage dessinent les contours d'entrepôts plus sûrs, plus efficaces et plus durables. L'intégration des technologies avancées, des matériaux de nouvelle génération et des approches prédictives transforme progressivement ce domaine traditionnellement conservateur.
Ces évolutions ne représentent pas simplement des améliorations incrémentales, mais une véritable révolution dans la conception, l'utilisation et la maintenance des infrastructures de stockage. Les rayonnages passent du statut de structures passives à celui de composants actifs et intelligents de l'écosystème logistique, capables de communiquer leur état, d'interagir avec leur environnement et de s'adapter aux besoins changeants.
Dans cette perspective, la réparation, le renforcement et le remplacement des racks ne sont plus des approches isolées, mais s'intègrent dans une stratégie globale de gestion du cycle de vie des équipements. Cette vision holistique, soutenue par des outils digitaux avancés, permet d'optimiser les décisions d'intervention en fonction de multiples paramètres : état technique des structures, contraintes opérationnelles, considérations économiques et environnementales.
Les entreprises spécialisées comme ROS France évoluent en conséquence, élargissant leur offre pour proposer des solutions intégrées couvrant l'ensemble du spectre, depuis la conception initiale jusqu'au démantèlement en fin de vie, en passant par l'inspection, la réparation et le renforcement. Cette approche globale répond aux attentes croissantes des gestionnaires d'entrepôts en matière de simplicité, d'efficacité et de responsabilité.
Sur le plan technologique, l'avenir verra probablement l'émergence de rayonnages encore plus intelligents et adaptatifs. Des concepts innovants sont déjà à l'étude, comme des structures modulaires capables de se reconfigurer automatiquement en fonction des besoins de stockage, ou des systèmes intégrant des matériaux à mémoire de forme pouvant absorber les chocs puis retrouver leur géométrie d'origine.
La dimension environnementale continuera également à gagner en importance, avec le développement de solutions toujours plus respectueuses des principes de l'économie circulaire. L'utilisation de matériaux recyclés ou biosourcés, la conception favorisant le démontage et la réutilisation, ainsi que l'optimisation de l'empreinte carbone tout au long du cycle de vie représentent des axes de développement prometteurs.
Enfin, l'intégration croissante des racks de stockage dans l'écosystème plus large de l'entrepôt connecté ouvrira de nouvelles perspectives en termes d'optimisation globale. La communication entre les rayonnages, les systèmes de manutention automatisés, les logiciels de gestion et les autres équipements permettra une orchestration harmonieuse de l'ensemble des flux logistiques, maximisant ainsi l'efficience opérationnelle tout en minimisant les risques.
Ces évolutions, bien que technologiquement avancées, restent fondamentalement au service d'objectifs essentiels : améliorer la sécurité des personnes, optimiser la performance logistique et réduire l'impact environnemental. Dans cette perspective, les innovations les plus pertinentes seront celles qui parviendront à concilier ces différentes dimensions, offrant des solutions véritablement durables au sens le plus large du terme.
Alors que nous avons exploré en détail les différentes approches de gestion des racks de stockage, de la réparation au remplacement en passant par le renforcement et la prévention, il convient maintenant de synthétiser ces éléments dans une vision globale et intégrée. Comment articuler ces différentes stratégies dans une approche cohérente ? Quels principes directeurs adopter pour optimiser la gestion de vos infrastructures de stockage ? C'est ce que nous allons aborder dans la conclusion de cet article.
Vers une gestion optimale des racks de stockage : l'approche intégrée
Au terme de cette analyse approfondie des différentes stratégies de gestion des racks de stockage, il apparaît clairement qu'aucune approche isolée ne peut répondre à l'ensemble des enjeux auxquels sont confrontés les gestionnaires d'entrepôts. La réparation, le renforcement et le remplacement constituent des options complémentaires, dont la pertinence dépend de multiples facteurs spécifiques à chaque situation. C'est précisément dans l'articulation judicieuse de ces différentes stratégies que réside la clé d'une gestion optimale des infrastructures de stockage.
L'approche intégrée que nous préconisons repose sur plusieurs principes fondamentaux. En premier lieu, elle s'appuie sur une connaissance précise et actualisée de l'état des installations. Les programmes d'inspection structurés, combinant contrôles visuels réguliers et technologies avancées de surveillance, fournissent les données essentielles pour des décisions éclairées. Cette dimension préventive constitue le socle d'une stratégie efficace, permettant d'identifier précocement les problèmes potentiels et d'intervenir avant qu'ils ne s'aggravent.
Par ailleurs, cette approche intégrée adopte une vision globale du cycle de vie des équipements. Plutôt que de considérer chaque intervention de manière isolée, elle s'inscrit dans une perspective de long terme, prenant en compte l'historique des structures, leur utilisation actuelle et les évolutions prévisibles des besoins logistiques. Cette vision temporelle élargie permet d'optimiser les décisions d'investissement et de maintenance, en équilibrant judicieusement les considérations immédiates et les objectifs stratégiques.
La dimension économique occupe naturellement une place centrale dans cette approche. Toutefois, l'analyse financière ne se limite pas au simple coût direct des interventions, mais intègre l'ensemble des impacts économiques : perturbations opérationnelles, risques assurantiels, durée de vie résiduelle des équipements, etc. Cette évaluation globale révèle souvent que la solution apparemment la plus économique à court terme n'est pas nécessairement la plus avantageuse dans une perspective plus large.
La sécurité demeure, bien entendu, une priorité absolue. L'approche intégrée place cet impératif au cœur de toutes les décisions, en s'appuyant sur des référentiels normatifs exigeants et des certifications reconnues. Le recours à des professionnels qualifiés, comme ROS France pour la réparation, garantit non seulement la conformité aux standards en vigueur, mais également une sécurité durable des installations.
Enfin, les considérations environnementales prennent une importance croissante dans cette vision intégrée. La prolongation de la durée de vie des équipements existants, à travers la réparation et le renforcement, s'inscrit parfaitement dans les principes de l'économie circulaire et contribue à réduire l'empreinte écologique des activités logistiques. Cette dimension, au-delà de son importance intrinsèque, répond également aux attentes croissantes des parties prenantes en matière de responsabilité environnementale.
Pour mettre en œuvre concrètement cette approche intégrée, plusieurs recommandations pratiques peuvent être formulées :
- Établir un inventaire détaillé et actualisé des installations, incluant les caractéristiques techniques, l'historique des interventions et l'état actuel de chaque élément.
- Mettre en place un programme d'inspection structuré, conforme aux recommandations de la norme NF EN 15635, en combinant contrôles visuels réguliers et technologies avancées de surveillance.
- Développer une matrice décisionnelle personnalisée, intégrant les spécificités de l'entrepôt, pour guider les choix entre réparation, renforcement et remplacement face à différents scénarios de dommages.
- Établir des partenariats durables avec des prestataires certifiés, capables d'offrir une gamme complète de solutions et de conseiller objectivement sur les options les plus adaptées à chaque situation.
- Former l'ensemble du personnel aux bonnes pratiques d'utilisation et de surveillance des racks, créant ainsi une véritable culture de la sécurité au sein de l'organisation.
- Intégrer la gestion des racks dans une stratégie plus large de maintenance des actifs, en coordination avec les autres équipements et systèmes de l'entrepôt.
L'évolution technologique ouvre des perspectives prometteuses pour cette approche intégrée. Les racks intelligents, les systèmes de surveillance connectés et les outils digitaux de gestion de la maintenance constituent des leviers puissants pour optimiser la gestion des infrastructures de stockage. Ces innovations, loin de remplacer l'expertise humaine, la complètent et la renforcent, permettant des décisions plus précises, plus rapides et mieux documentées.
En définitive, la gestion optimale des racks de stockage ne réside pas dans le choix exclusif d'une stratégie particulière, mais dans la capacité à combiner judicieusement différentes approches en fonction des circonstances spécifiques. Cette vision intégrée, alliant rigueur méthodologique, expertise technique et ouverture aux innovations, permet de concilier les impératifs parfois contradictoires de sécurité, d'efficacité opérationnelle, de performance économique et de responsabilité environnementale.
Face aux défis complexes de la logistique moderne, cette approche équilibrée et pragmatique offre aux gestionnaires d'entrepôts un cadre structurant pour des décisions éclairées, garantissant la pérennité et la sécurité de leurs infrastructures de stockage. En adoptant cette vision globale, ils transforment la maintenance des racks d'une contrainte réactive en un levier stratégique d'optimisation et de création de valeur.
Pour toute question concernant vos installations de stockage ou pour obtenir un diagnostic professionnel, n'hésitez pas à nous contacter. Notre équipe d'experts se tient à votre disposition pour vous accompagner dans la gestion optimale de vos racks de stockage.